Your cart is currently empty!
How To Prepare for a Cleanroom Inspection
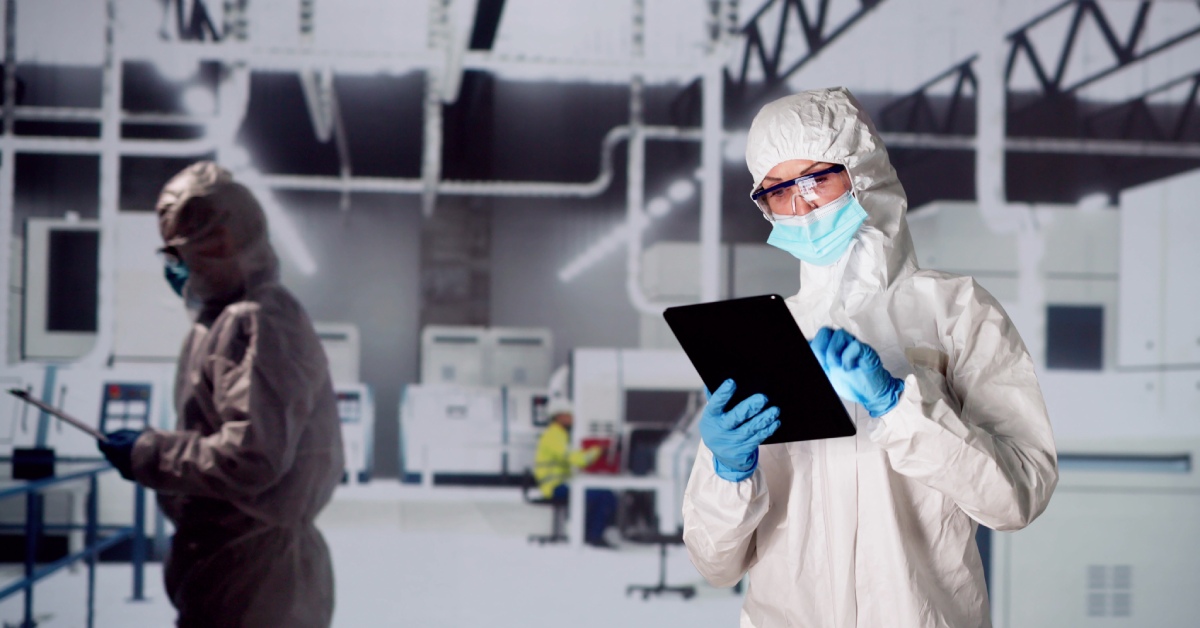
Cleanroom inspections are crucial for maintaining high standards and avoiding contamination in manufacturing environments. Proper planning and execution can make the process smooth and efficient.
Different ways include training your staff, stocking up on cleanroom supplies, and conducting mock surveys. Here’s everything you need to know about how to prepare for a cleanroom inspection
1. Understand the Cleanroom Inspection Process
The first step in preparing for a cleanroom inspection is to understand the process. Cleanroom inspections typically involve a thorough examination of your facility’s layout, equipment, procedures, and documentation. Inspectors will check for compliance with industry standards and regulations to ensure that your cleanroom meets the required cleanliness levels.
Industry-Specific Focus
Familiarize yourself with the specific standards applicable to your industry. For example, inspectors may focus on how well you control chemical fumes or how well you manage hazardous materials.
Regulatory Standards
Understand that each cleanroom has to follow different regulatory standards depending on its usage and the products you manufacture. It may be worth reviewing standards such as ISO 14644-1, which classifies cleanrooms based on their air cleanliness levels. Compliance with these standards is a critical aspect of maintaining product quality and safety.
Inspection Criteria
Inspectors often examine several key aspects. Here are a few of them to consider when preparing:
- Ensure that air systems function optimally to control contamination.
- Regularly monitor surface cleanliness using standard cleaning protocols.
- Verify documentation and adherence to standard operating procedures (SOPs).
- Ensure that staff comply with gowning and hygiene protocols to prevent contamination.
2. Train Your Staff
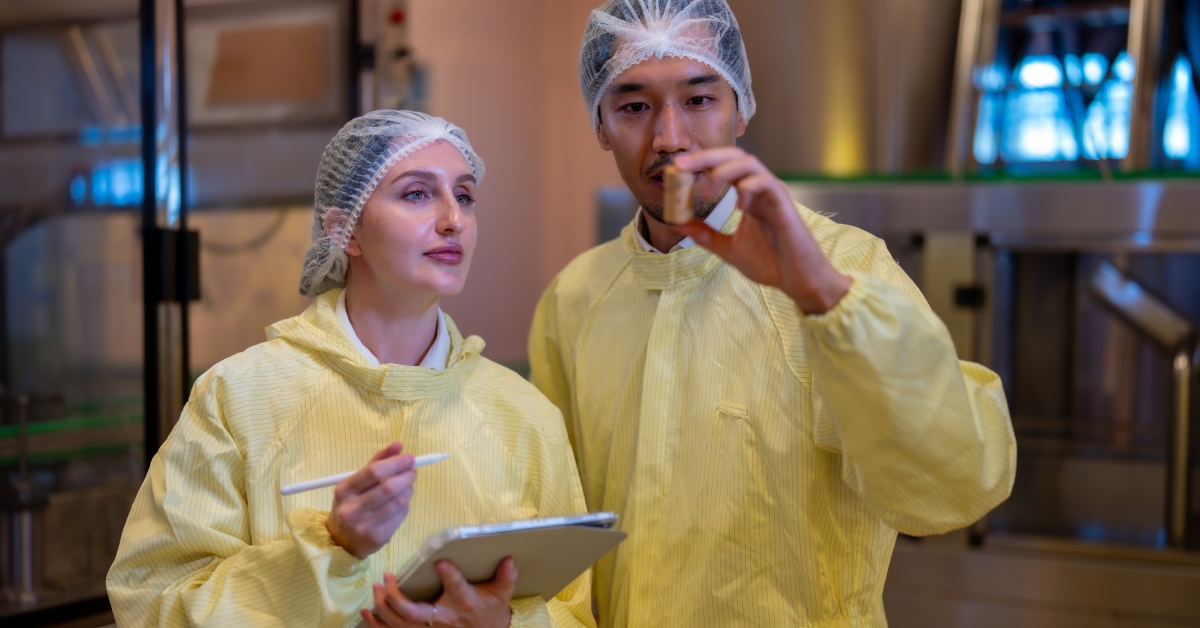
Another important tip on how to prepare for a cleanroom inspection is training your staff. Proper training ensures that everyone understands the importance of cleanliness and adheres to the protocols necessary to maintain it. Regular training sessions can reinforce these practices and keep your team updated on any changes in standards or procedures.
Training Essentials
Start by reviewing your current training materials and updating them if necessary. Confirm that all employees, from entry-level workers to management, have received training on cleanroom protocols. This includes proper gowning procedures, hand hygiene, and the correct use of equipment.
Continuous Learning
Conducting regular training sessions and refresher courses can help you maintain a high level of compliance and readiness among your staff. Consider involving external experts for specialized training sessions to provide additional insights and best practices.
Employee Engagement
Engage your employees by involving them in training programs. Organize workshops, Q&A sessions, and practical demonstrations to make the training more interactive. Encourage staff to provide feedback on the training sessions, which you can use to further enhance the training process.
3. Stock Up on Cleanroom Lab Supplies
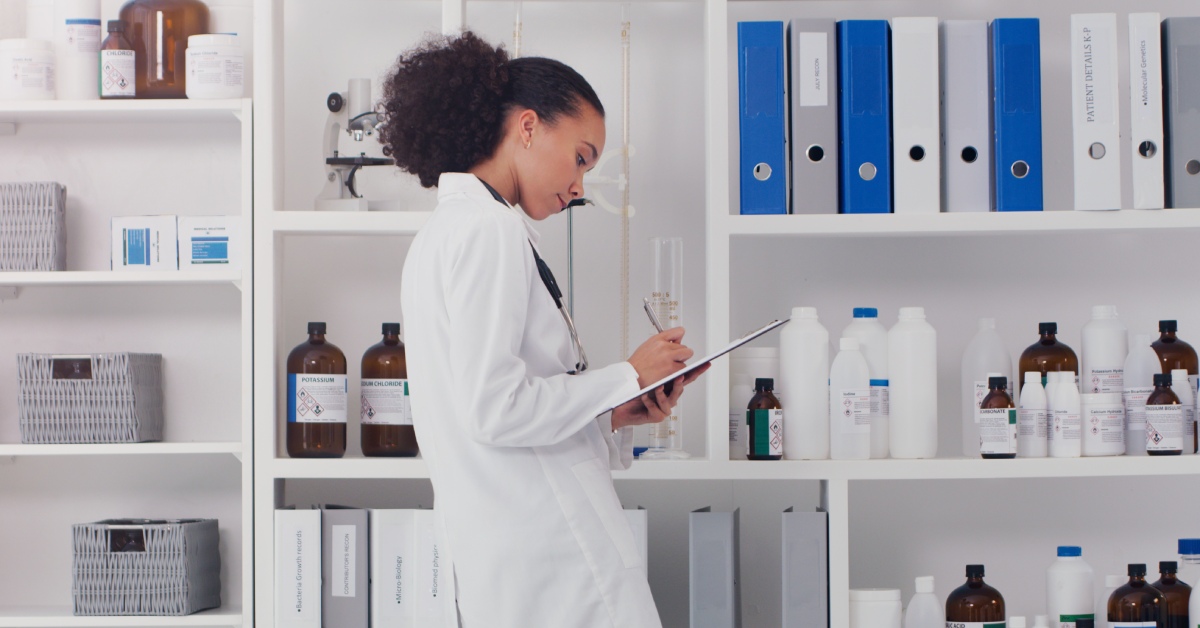
Having the right supplies is essential for maintaining a cleanroom environment. Make sure that you have an adequate stock of cleanroom lab supplies, including gloves, gowns, masks, and cleaning agents. Regular inventory checks can prevent shortages and ensure that you’re always prepared for an inspection.
Sourcing Supplies
When sourcing supplies, consider reputable suppliers who specialize in cleanroom products. A scientific chemical company like Post Apple Scientific can provide high-quality cleaning agents and other essential supplies.
Inventory Management
Regularly review your inventory and replenish supplies as needed. This proactive approach can prevent last-minute scrambles.
Quality Control
Perform quality checks on the supplies you use to confirm they meet the required standards for your cleanroom. Regularly audit your suppliers to make sure they comply with industry-specific regulations. Document any discrepancies and address them promptly.
4. Conduct a Mock Survey
A mock survey helps your company identify potential issues before the actual inspection. By simulating an inspection, you can evaluate your cleanroom’s compliance with standards and identify areas that need improvement.
Simulating Inspections
During the mock survey, focus on the same areas that inspectors will examine. Check for cleanliness, proper documentation, and adherence to protocols. Involve your staff in the process so that they understand what to expect and how to respond during the actual inspection.
Action Plan
Document the findings of the mock survey and create an action plan to address any identified issues. Regularly conducting mock surveys can help you maintain a high level of readiness.
Frequency of Mock Surveys
Schedule mock surveys periodically throughout the year rather than just before an anticipated inspection. Consistent mock surveys reinforce the importance of ongoing compliance.
5. Document the Results
Proper documentation is a critical aspect of cleanroom inspections. Inspectors will review your records to confirm that you are consistently maintaining the required standards. Keeping detailed and accurate records can demonstrate your commitment to cleanliness and compliance.
Documentation Strategy
Make sure that all procedures and protocols are well-documented and easily accessible. This includes cleaning schedules, maintenance logs, and training records. Regularly review and update your documentation to reflect any changes in procedures or standards.
Digital Solutions
Consider implementing a digital documentation system to streamline record-keeping and ensure all information is up-to-date. This can make it easier to access and share records during an inspection, reducing the time and effort required to demonstrate compliance.
Audits and Reviews
Conduct internal audits of your documentation periodically to avoid overlooking anything. Reviews by a third party can add an extra layer of assurance. Organized and detailed records simplify the inspection process and show a clear commitment to maintaining cleanroom standards.
6. Conduct External Surveys
External surveys conducted by third-party organizations can provide an objective assessment of your cleanroom. These surveys can identify areas for improvement. External surveys can also provide valuable insights and recommendations for enhancing your cleanroom’s performance.
Selecting a Third-Party Organization
When selecting a third-party organization for an external survey, choose one with expertise in your industry. They will have a better understanding of the specific requirements and challenges you’ll face.
Continuous Improvement
Use the findings from external surveys to inform your continuous improvement efforts. Implementing their recommendations can enhance your cleanroom’s performance and ensure that you’re always prepared for inspections.
Build Relationships
Foster strong relationships with external auditors and surveyors. Their ongoing feedback and collaboration can significantly benefit your continuous improvement processes, making the journey toward compliance smoother and more effective.
Cleanroom inspections are a necessary part of maintaining contamination control in various industries. Sourcing lab supplies from reputable companies like Post Apple Scientific, along with following all the other preparation tips, will help you stay prepared for future inspections.
Leave a Reply