The world of chemistry is full of fascinating processes, and distillation is one of the most intriguing. This method, often seen in both industrial applications and high school science labs, involves separating components from a liquid mixture by selective evaporation and condensation. Understanding the nuances of the distillation process of chemicals can provide valuable insights into its applications and importance.
The Basics of Chemical Distillation
At its core, distillation is a method used to separate liquids based on differences in their boiling points. When you heat a liquid, it turns into vapor. If you cool this vapor, it condenses back into a liquid. Distillation leverages these phase changes to separate components of a mixture.
For instance, in a mixture of water and alcohol, alcohol boils at a lower temperature than water. Heating the mixture allows the alcohol to vaporize first, which makes it easy to separate. Distillation is not only about separation; it’s also about purification. By isolating a component, you effectively remove impurities and improve the purity of the collected substance.
Types of Distillation Methods
There are several types of distillation methods, each with its own set of applications and benefits. The most common form is simple distillation, which is typically used when you need to separate components with differing boiling points. It’s a straightforward process that is often used in laboratories to purify liquids like ethanol.
Fractional distillation is another popular method. Unlike simple distillation, it involves a fractionating column, which allows for the separation of components with closer boiling points. The petroleum industry frequently uses this method to separate crude oil into various useful fractions like gasoline, diesel, and kerosene. The fractionating column helps achieve better separation by increasing the surface area and allowing multiple condensation and evaporation cycles.
Finally, there’s steam distillation, which is typically used for extracting essential oils from plants. This method involves passing steam through plant material to vaporize volatile compounds. Factory workers prefer steam distillation for compounds that decompose at high temperatures and are commonly used in the fragrance and flavor industries.
The Role of Temperature and Pressure
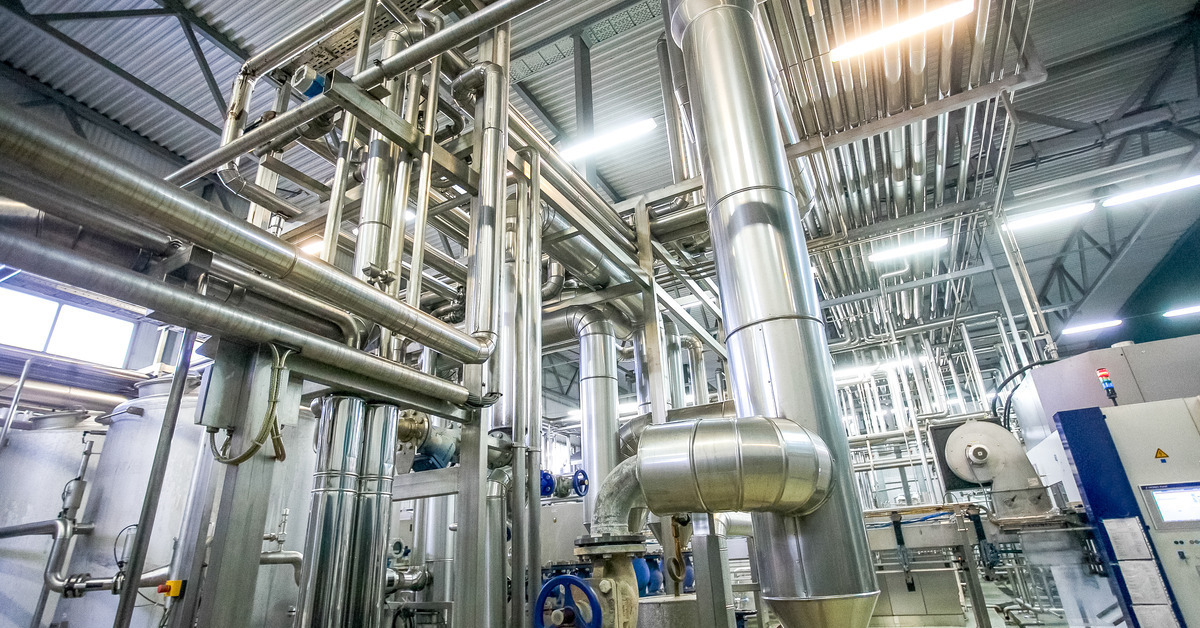
Temperature and pressure play a significant role in the distillation process. These factors determine the rate of evaporation and condensation, which affect both the efficiency and the quality of the separation. In general, the higher the temperature, the quicker the evaporation. However, if the temperature is too high, you may risk decomposing heat-sensitive components.
Pressure is equally important, particularly in vacuum distillation. By reducing the pressure within the distillation apparatus, you effectively lower the boiling point of the components. This is particularly useful for substances that boil at very high temperatures, making distillation more energy-efficient while reducing the risk of thermal decomposition.
Controlling both temperature and pressure requires sophisticated equipment and a deep understanding of the distillation process. Industries often rely on automated systems to maintain the right conditions, which ensures consistent quality and efficiency in their distillation operations. Whether you’re distilling in a lab or on an industrial scale, it’s important to master the interplay between these factors to achieve successful separation.
Applications Across Various Industries
Distillation is a versatile process with applications in numerous industries. In the pharmaceutical industry, it’s used to purify and concentrate active ingredients, which ensures the production of effective medications. The food and beverage sector relies on distillation to produce alcoholic beverages, flavors, and essential oils.
In the petrochemical industry, distillation is necessary for refining crude oil into valuable fuels and chemicals. The process allows for the separation of complex mixtures into usable products, which is vital for meeting global energy demands. The process is also used in water treatment plants to produce distilled water that is free from impurities and contaminants.
Challenges in Distillation
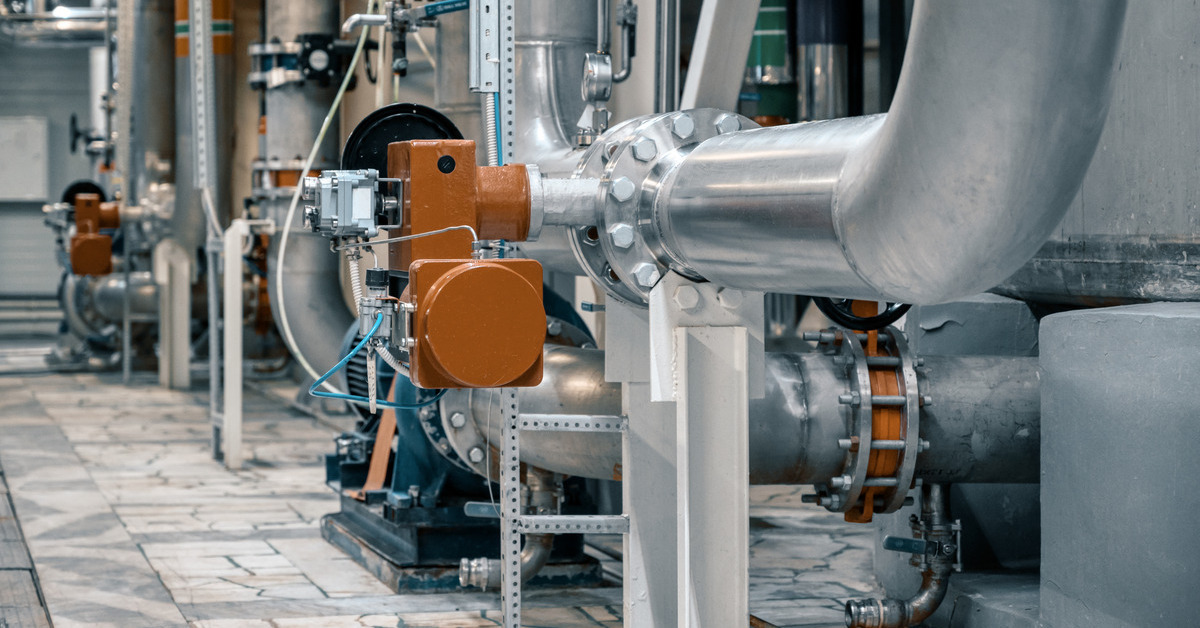
Despite its many advantages, the distillation process of chemicals isn’t without challenges. Energy consumption is a primary concern, as the process typically requires significant heat input, especially in industrial settings. Finding ways to improve energy efficiency while maintaining product quality is an ongoing challenge.
Another challenge is the potential for contamination during the process. Even minor impurities can affect the quality of the final product, particularly in high-purity applications like pharmaceuticals. Ensuring that equipment is clean and well-maintained is essential to preventing contamination and achieving the desired purity levels.
Innovations in Distillation Technology
Over the years, the distillation process has seen numerous innovations aimed at improving efficiency and overcoming challenges. One such advancement is the development of membrane distillation, which uses a semi-permeable membrane to separate components. This method offers the potential for lower energy consumption compared to traditional distillation.
Another innovation is the integration of distillation with other separation techniques, such as adsorption or extraction. These hybrid processes can enhance separation efficiency and reduce energy requirements. For example, pervaporation combines distillation and membrane technology to separate azeotropic mixtures that are difficult to separate through conventional methods.
Lab Chemicals for Distillation
Sourcing high-quality lab chemicals is necessary for those involved in the distillation process. Whether you’re conducting research or are involved in production, the quality of your chemicals can significantly impact the success of your distillation efforts. It’s important to choose a reputable supplier that offers a wide range of chemicals suitable for your specific needs.
One option is to buy lab chemicals online from Post Apple Scientific. We offer a comprehensive selection of chemicals and equipment, which makes it easy to find what you need for your distillation projects. Furthermore, we test everything in our store for purity to ensure you achieve accurate results. With online purchasing, you can access high-quality products conveniently and efficiently.
Future Trends in Distillation
Ongoing advancements in technology and increasing demand for sustainable practices will shape the future of the distillation process. Continued innovation in membrane technology and hybrid processes will drive improvements in efficiency and energy use. These advancements will make distillation more accessible and cost-effective across various industries.
Automation and digitalization are also expected to play a significant role in the future of distillation. The integration of smart technologies and real-time data analytics can enhance process control and optimization, leading to more precise and efficient separation processes. This trend is likely to benefit industries seeking to improve productivity and product quality.
Advancements in distillation bacan4d continue to open new possibilities for industries seeking to improve efficiency and sustainability. By understanding these trends, businesses can make smart decisions and stay competitive in a rapidly evolving landscape.